Stucco application is a time-consuming and labor-intensive process. You’ll want to hire a stucco contractor who is efficient and able to deliver high-quality work on schedule.
Ask potential contractors for references and reviews from previous clients. This will help you gauge the contractor’s work ethic and customer satisfaction levels. Click the Philadelphia Stucco Contractor to learn more.
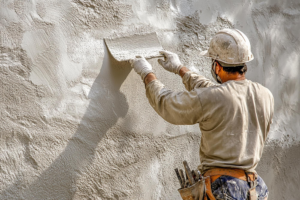
Request a written estimate that details the scope of work, timeline, and payment terms. Also, inquire about the warranty coverage provided by the contractor.
Experience
When hiring a Stucco Contractor, it is vital that you hire someone with experience. In addition to their licensing and insurance requirements, a stucco contractor with experience will be able to address any issues that arise during the project more quickly and efficiently. Moreover, an experienced contractor will be able to provide advice about the best materials to use for your specific project. They can also recommend the right application process to achieve the desired results.
A good stucco contractor should have a solid portfolio of past projects and client references. Requesting to see their work will allow you to assess whether their style matches your vision. It will also give you an idea about the quality of their craftsmanship and attention to detail. You should also look for a warranty on their work and consider the terms of the warranty, as well as maintenance services that are available after the job is completed.
Stucco is a unique material, and it requires proper application to ensure long-lasting beauty and durability. An inexperienced contractor may apply the stucco unevenly, leading to cracks or other surface problems. An experienced contractor will be able to avoid these mistakes and ensure that the finish is flawless.
Moreover, a skilled contractor will pay close attention to substrate preparation and mixing of the stucco materials. They will be able to deliver a high-quality finish that is durable and long-lasting. Choosing a contractor with superior workmanship is just as important as selecting the right materials for your project.
Local contractors are often more familiar with the challenges and regulations that may affect your project. They are also more likely to be accessible should any issues arise during or after the project is complete. They can address these issues faster and more effectively than a national company that may not have the same level of familiarity with your area.
When looking for a Stucco Contractor, it is essential that you take your time to find one with a strong reputation in the community and who can offer the best value for your money. Look for a variety of factors, including licensing and insurance requirements, years of industry experience, a strong portfolio with client references, effective communication skills and excellent customer service, and a clear understanding of contracts and payment terms.
Warranty
A good stucco contractor will offer a warranty for their work. This is important because it gives you peace of mind knowing that if something goes wrong with your stucco, they will repair it at no cost to you. A warranty can also increase the value of your home, making it more attractive to potential buyers.
Before choosing a stucco contractor, it is essential to check their work history and references. This will help you decide whether they are the right fit for your project. You can also find out more about the quality of their work by reading online reviews and asking for referrals. You can also request a copy of their contract before hiring them. This will detail the scope of the work, payment terms, and warranties.
One of the most important factors to consider is the length and coverage of a stucco warranty. A solid warranty should include both material and workmanship problems for a set term. In addition, it should cover the cost of repairs and replacements if necessary. A warranty can protect your investment and ensure that you receive high-quality craftsmanship.
Stucco is a popular choice for building exteriors, as it adds value and beauty to your home. However, like any other type of construction material, it can be damaged over time. A good stucco contractor will be able to provide you with a strong and reliable warranty to protect your investment.
The price of a stucco warranty varies depending on the duration and coverage. Some warranty providers offer up to 10 years of repair coverage, while others have shorter plans. You should always choose a warranty that is designed to suit your needs.
Another factor to consider is the transferability of a warranty. Many companies do not allow the warranty to be transferred to a new homeowner. This can be a major problem, as the transferability of a warranty can impact a property’s resale value.
Choosing the right stucco contractor is a crucial decision for homeowners, realtors, and real estate agents. It is important to look for a company that has a proven track record of quality work and customer satisfaction. In addition, a good stucco contractor will provide excellent after-sale service.
Communication
A stucco contractor should be able to communicate clearly and concisely with clients. This is a vital factor in establishing trust and credibility. Contractors should also be able to answer questions promptly and explain technical information in an understandable manner. This ensures that all parties are on the same page throughout the project.
A reputable contractor will be able to provide references and online reviews from previous clients that speak to their work ethic and level of customer satisfaction. It is recommended to contact these individuals directly and inquire about their experience with the contractor, including the quality of the work, timeliness, and cost.
Getting a detailed written estimate from a stucco contractor is important to avoid any misunderstandings and ensure transparency. This document should include a scope of work, an estimated timeline for completion, a payment schedule, and warranty details. In addition, it should detail the type of materials and their price, as well as any additional charges or fees that may be incurred.
It is important to check that the stucco company you choose has a business license and insurance coverage before beginning any work on your home. Word of mouth or handshake deals are not legally binding and can leave you open to financial loss if something goes wrong during the course of the work. Moreover, a licensed and insured stucco company will be able to offer you the best possible service as they will be held accountable for their actions.
Stucco contractors can be found in a variety of locations, from local businesses to online review platforms. It is beneficial to hire a contractor who is located in your area as this can cut down on the time it takes to bring workers and materials to the job site. In addition, a local contractor will be familiar with the unique challenges that stucco faces in your specific climate.
Hiring a stucco contractor is a big investment in your home, and you should take the time to find one who will be able to meet your needs. Look for a company that has years of experience, provides clear communication, and offers a competitive warranty. By doing so, you can be sure that your exterior stucco will last for many years to come and add to the beauty of your home.
Pricing
When hiring a stucco contractor, it’s important to consider the quality of their work as well as the prices they charge. Poor stucco work can cause severe damage to your home and require extensive remediation, which is both time consuming and expensive. This is why it’s important to find a contractor who has the skills and experience to provide high-quality results.
A quality contractor will have a strong portfolio of previous work to show their craftsmanship and attention to detail. They should also be able to answer questions about their work and provide client references. It’s also important to find out if the contractor has the necessary licenses and insurances for the job, as these can affect pricing.
Stucco contractors generally charge by the square foot for their services, but there are a few factors that can affect this price. For example, the location of the project will affect how much it costs to get materials to the site. This can be a significant cost if the project is located far from the contractor’s business location.
Another factor is the type of material used. Some manufacturers offer products that are more expensive than others, but these higher-quality materials often have advantages such as reduced shrinkage cracking or a more resilient finish. In some cases, the additional costs can make the difference between a good job and a poor one.
Finally, the amount of labor required will influence how much it costs to complete the work. Some stucco contractors will roll the price of materials and labor into one price, while others may choose to charge by the hour. This is common for larger repairs that may require a lot of labor, such as water damage repair or major surface prep.
A good stucco contractor will be able to explain the different factors that go into their pricing and how they apply them to each project. They should also be able to give you a timeline for the completion of the work and a detailed breakdown of expenses. This will allow you to compare estimates more effectively and make the best decision for your needs.